Introduction
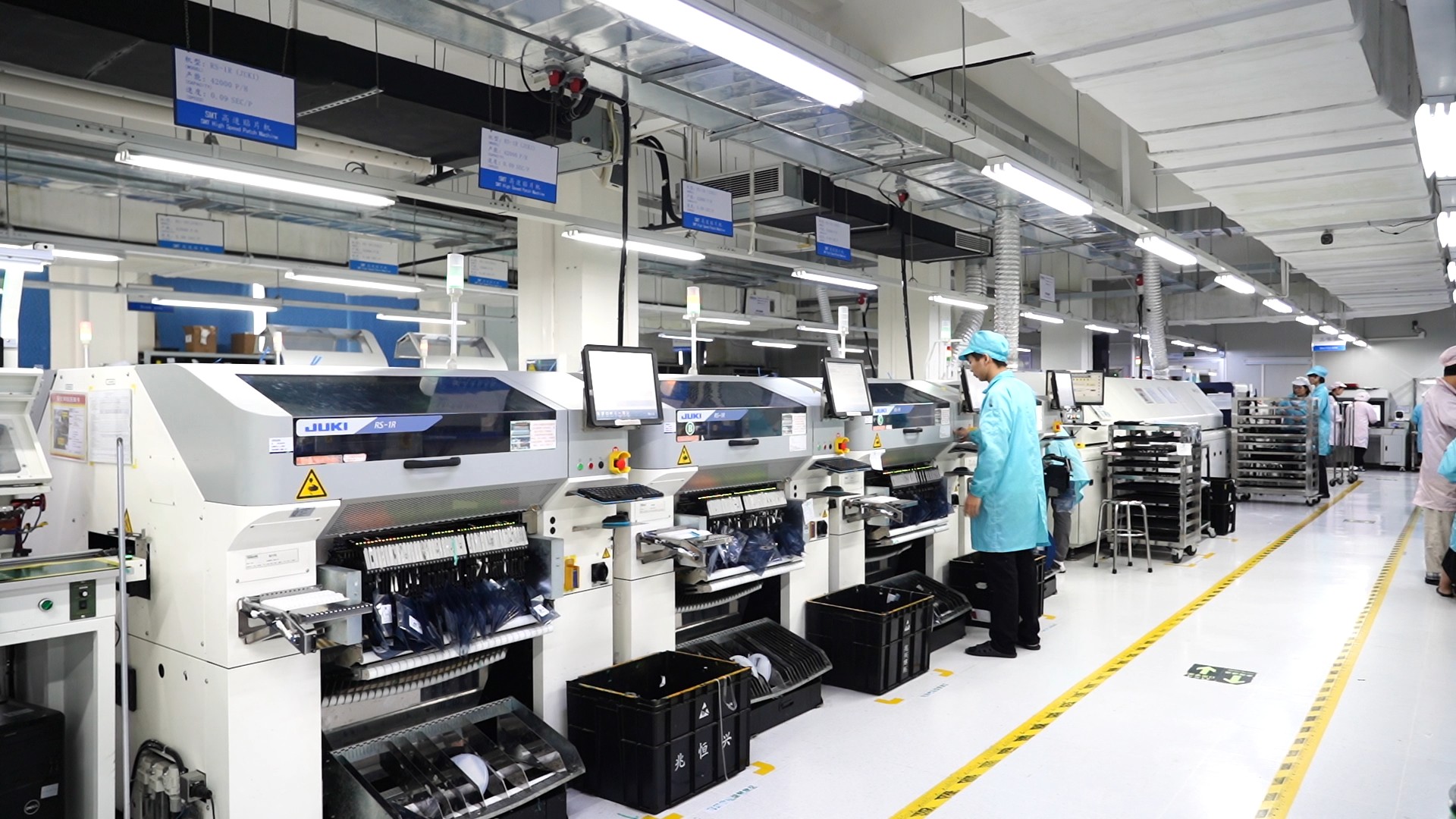
In the fast-paced world of electronics, understanding the intricacies of PCB assembly is crucial for manufacturers and designers alike. The costs associated with circuit card assembly can vary widely based on several factors, making it essential to grasp how these expenses are structured. By delving into the nuances of PCB board assembly, businesses can make informed decisions that optimize their budget while maintaining quality.
Understanding PCB Assembly Costs
PCB manufacturing costs are influenced by a myriad of elements including design complexity, material selection, and production volume. Each step in the PCB assy process—from prototyping to final assembly—contributes to the overall expense, which can significantly impact a project's bottom line. By breaking down these components and understanding their implications, companies can better strategize their expenditures in circuit board manufacturing.
The Importance of Quality in PCB Manufacturing
Quality should never be an afterthought when it comes to PCB board assembly; it’s a foundational element that determines product reliability and longevity. High-quality materials and precise manufacturing processes not only enhance performance but also reduce long-term costs related to repairs or replacements. In an industry where failure can lead to catastrophic results, investing in quality during the PCB assy phase is non-negotiable.
Cost-Saving Strategies for PCB Board Assembly
To navigate the often-treacherous waters of PCB assembly costs, manufacturers must adopt effective cost-saving strategies without compromising on quality. This includes optimizing designs for manufacturability, selecting appropriate materials that balance cost with performance, and leveraging technology for efficiency gains in production processes. By implementing these strategies thoughtfully, businesses can achieve significant savings while ensuring that their circuit card assemblies meet industry standards.
What is PCB Assembly?
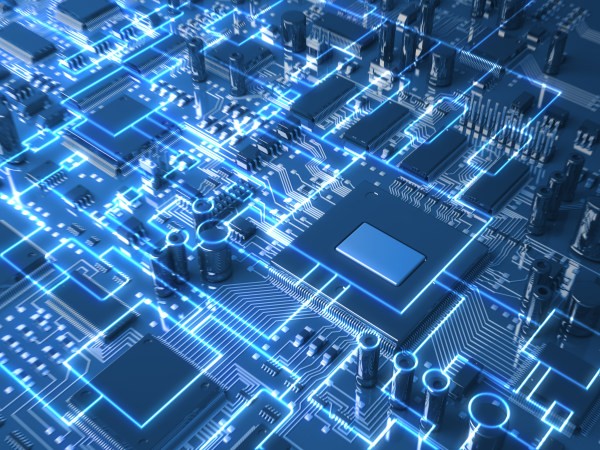
PCB assembly, or printed circuit board assembly, is the process of connecting electronic components to a circuit board to create functional electronic devices. This process transforms a bare PCB into a fully operational product, ready for use in various applications like consumer electronics, automotive systems, and industrial machinery. Understanding the nuances of PCB assembly is essential for anyone looking to navigate the complexities of circuit card assembly effectively.
Basics of Circuit Card Assembly
At its core, circuit card assembly involves several steps that ensure all components are properly placed and soldered onto the PCB. The journey begins with designing the layout using specialized software, which dictates where each component will go on the board. Following this design phase, manufacturers utilize techniques such as surface mount technology (SMT) and through-hole technology to attach components securely during the PCB assembly process.
The quality of circuit card assembly directly impacts the functionality and reliability of electronic devices. A well-executed PCB assy minimizes defects and enhances performance while reducing long-term costs associated with repairs or replacements. Therefore, understanding these basics is crucial for both manufacturers and clients alike.
Key Processes in PCB Manufacturing
PCB manufacturing encompasses several key processes that collectively contribute to successful PCB board assembly. Initially, raw materials are prepared by etching copper layers onto a substrate material—usually made from FR-4 or other dielectric materials—to form conductive pathways. After this initial step, additional processes like drilling holes for component leads and applying solder mask layers protect against shorts and enhance durability are executed.
Once these foundational steps are complete, it’s time for component placement—a critical phase in which automated machines place components precisely according to the design specifications from earlier stages. Following placement comes soldering; this can be done through reflow soldering or wave soldering methods depending on whether SMT or through-hole components are used in the PCB assy process. Each step must be meticulously executed to ensure high-quality outcomes in circuit board manufacturing.
Different Types of PCB Assy
There are several types of PCB assy tailored to meet various industry needs—each with its unique characteristics and advantages. For instance, single-sided PCBs have components mounted on one side only; they’re simple yet effective for many basic applications like household appliances or lighting fixtures. On the other hand, double-sided PCBs allow for more complex designs since they can accommodate components on both sides.
Moreover, multilayer PCBs take complexity up a notch by stacking multiple layers together; these boards are indispensable in advanced electronics such as smartphones or computers where space-saving designs are essential without compromising performance. Understanding these different types helps businesses choose appropriately based on their specific requirements during the procurement process from a reliable PCB board manufacturer.
Choosing the Right PCB Board Manufacturer
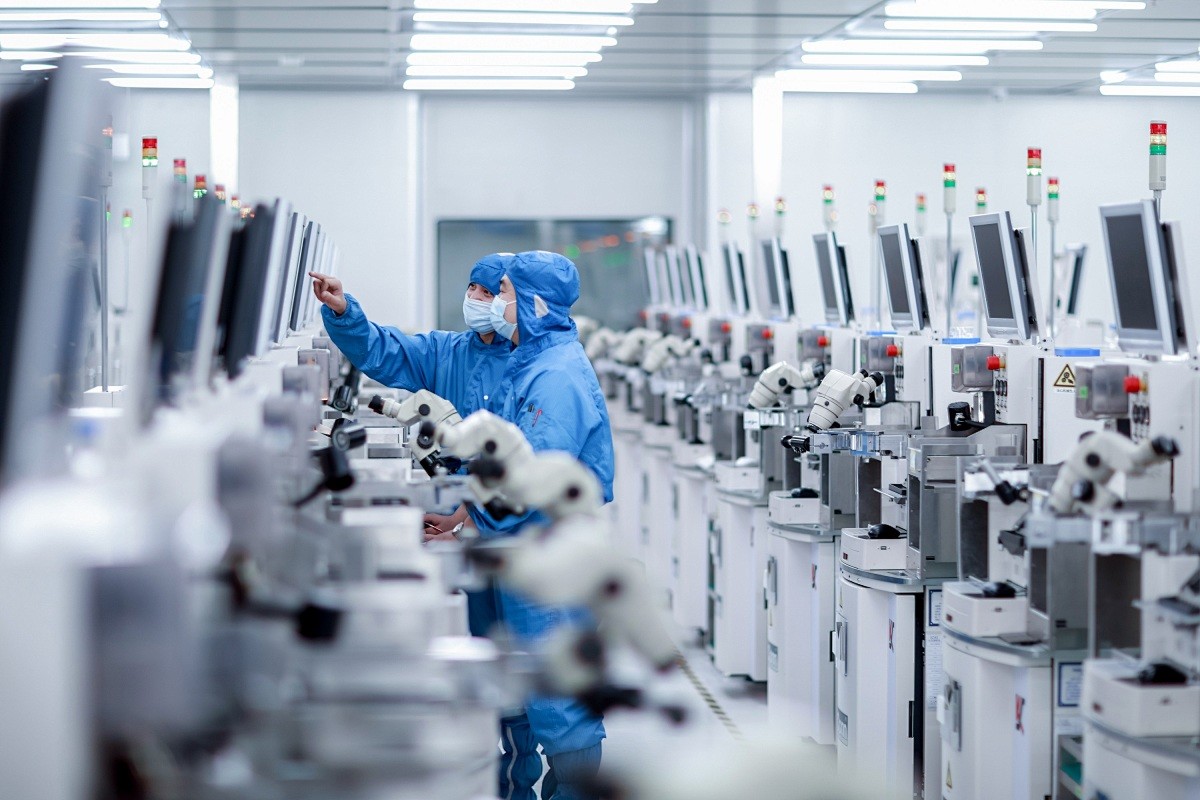
Selecting the right PCB board manufacturer is crucial for ensuring quality and cost-effectiveness in your circuit card assembly projects. With numerous options available, it's essential to evaluate manufacturers based on specific criteria that align with your project needs. A well-chosen PCB manufacturing partner can significantly influence the overall success of your PCB assembly endeavors.
Factors to Consider in Selection
When considering a PCB board manufacturer, several factors come into play, including experience, capabilities, and certifications. Look for a manufacturer with a proven track record in circuit board manufacturing that demonstrates expertise in various types of PCB assy processes. Additionally, ensure they have the necessary certifications such as ISO standards, which indicate their commitment to quality and reliability.
Another critical aspect is their ability to handle different volumes of production while maintaining consistency in quality for both small and large runs of PCB assembly. Communication is key; you want a manufacturer who is responsive and willing to collaborate on design modifications or troubleshooting during the assembly process. Finally, consider their pricing structure—transparency here can save you from unexpected costs down the line.
Benefits of Local vs. Global Manufacturers
Choosing between local and global manufacturers for your PCB board assembly comes with its own set of advantages and disadvantages. Local manufacturers often provide quicker turnaround times due to proximity, allowing for faster prototyping and revisions if needed during circuit card assembly processes. This can be particularly beneficial for startups or businesses looking to innovate rapidly without long lead times.
On the other hand, global manufacturers may offer lower production costs due to economies of scale or access to cheaper materials; however, this can sometimes come at the expense of longer shipping times and potential communication barriers. It's essential to weigh these factors against your project's specific needs—if rapid iteration is vital, local might be best; if cost savings are paramount, global could be advantageous.
How Bensun Technology Stands Out
Bensun Technology distinguishes itself as a leading player in the realm of PCB manufacturing by combining advanced technology with exceptional customer service tailored specifically for circuit board manufacturing needs. Their state-of-the-art equipment ensures precision during every stage of pcb assembly while maintaining competitive pricing without compromising quality—a win-win scenario!
Moreover, Bensun's commitment to sustainability sets them apart from many competitors; they prioritize eco-friendly materials in their pcb assy processes which not only benefits the environment but also appeals to increasingly eco-conscious consumers and businesses alike. With a strong focus on continuous improvement through innovation and automation in pcb board assembly practices, Bensun Technology stands ready to meet diverse client needs efficiently.
Leveraging Technology for Cost Efficiency
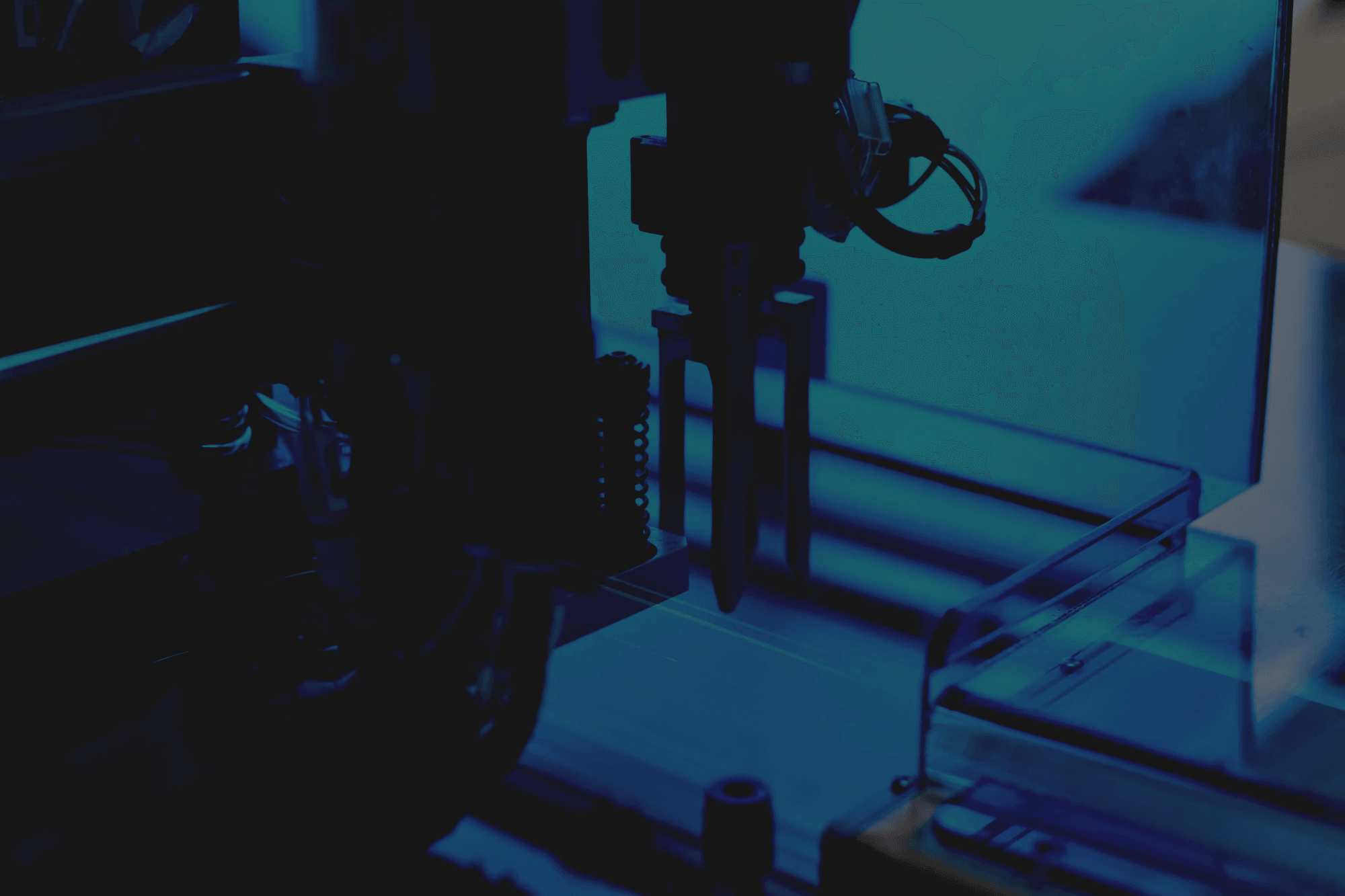
In the rapidly evolving world of PCB assembly, leveraging technology is essential for enhancing cost efficiency while maintaining quality. The integration of advanced equipment and automation into circuit board manufacturing processes has transformed the landscape, allowing manufacturers to streamline operations and reduce expenses. Bensun Technology exemplifies how innovation can lead to significant savings in PCB board assembly.
Advanced Equipment in PCB Board Assembly
Advanced equipment plays a pivotal role in optimizing the PCB assembly process. High-precision machines, such as pick-and-place robots and automated soldering systems, enable manufacturers to achieve greater accuracy and speed during circuit card assembly. This not only reduces labor costs but also minimizes errors, leading to higher-quality products that ultimately save money on rework and waste.
Moreover, modern inspection technologies like automated optical inspection (AOI) ensure that any defects are caught early in the manufacturing process. By investing in state-of-the-art machinery, PCB board manufacturers can significantly enhance their production capabilities while reducing turnaround times. The result is a more efficient workflow that allows for quicker response times to customer demands without sacrificing quality.
The Role of Automation in Cost Reduction
Automation has become a game-changer in the realm of PCB assembly, driving down costs while boosting productivity. By automating repetitive tasks within circuit board manufacturing, companies can allocate human resources to more complex problem-solving roles that require creativity and critical thinking. This shift not only enhances workforce satisfaction but also leads to better overall outcomes for the business.
Furthermore, automation reduces human error—one of the most significant contributors to increased costs in PCB assy processes. With machines performing tasks with consistent precision, manufacturers experience fewer defects and lower material waste rates. As a result, businesses can enjoy substantial long-term savings by implementing automated solutions throughout their operations.
Bensun Technology’s Innovative Solutions
Bensun Technology stands out as a forward-thinking leader in the field of PCB manufacturing by integrating cutting-edge solutions into their production lines. Their commitment to innovation is evident through their use of advanced robotics and AI-driven software that optimizes every stage of pcb board assembly—from design through final inspection. This holistic approach ensures that each circuit card assembly meets stringent quality standards while remaining cost-effective.
Additionally, Bensun’s focus on sustainable practices further enhances their value proposition; they utilize eco-friendly materials and energy-efficient processes that not only reduce costs but also appeal to environmentally conscious clients. By choosing Bensun Technology as your pcb board manufacturer partner, you’re not just investing in high-quality products; you’re also embracing a future where technology drives efficiency without compromising on sustainability or ethics.
Evaluating Material Costs and Choices
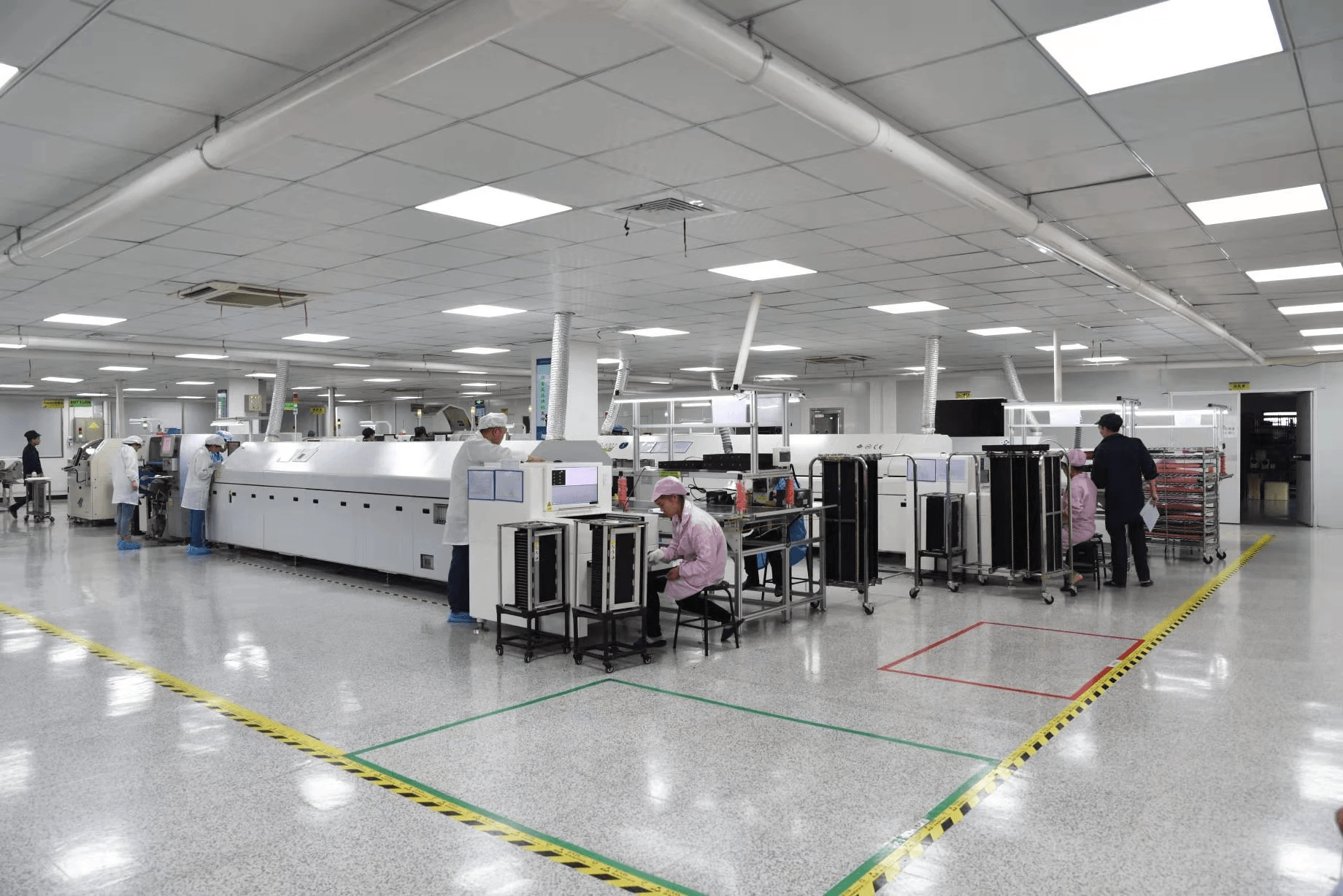
How Material Affects PCB Manufacturing Costs
The materials used in PCB manufacturing play a pivotal role in determining the final cost of production. For instance, high-performance substrates or specialized laminates can drive up expenses due to their superior properties but may be necessary for specific applications. Additionally, fluctuations in raw material prices can affect the cost of circuit board manufacturing, making it crucial for manufacturers to stay informed about market trends and adjust their sourcing strategies accordingly.
Moreover, selecting the right balance between cost-effective materials and high-quality components is vital for achieving a successful PCB assy outcome. While cheaper alternatives might seem appealing initially, they could lead to higher failure rates and increased warranty claims down the line. Therefore, investing in quality materials often pays off by reducing long-term costs associated with repairs and replacements.
Sustainable Materials in Circuit Board Manufacturing
As environmental concerns take center stage across various industries, sustainable materials are becoming increasingly important in circuit board manufacturing. Manufacturers are now exploring eco-friendly options such as biodegradable substrates or recycled components that not only reduce environmental impact but can also be cost-effective over time. By opting for sustainable materials in PCB assembly, companies can enhance their brand image while potentially lowering costs associated with waste disposal.
Incorporating sustainable practices into PCB board assembly doesn’t just benefit the planet; it can also attract customers who prioritize environmentally responsible products. Additionally, some governments offer incentives or grants for businesses that adopt green technologies or practices—making sustainability not just an ethical choice but a financially savvy one as well. Thus, manufacturers should keep an eye on emerging sustainable materials that could revolutionize their approach to circuit card assembly.
Tips for Reducing Material Waste
Reducing material waste is a win-win strategy that benefits both your bottom line and the environment during PCB manufacturing processes. One effective method is implementing lean manufacturing principles which focus on minimizing waste without sacrificing productivity—this includes optimizing layouts and workflows within your production line to ensure maximum efficiency during PCB assy operations.
Another practical tip involves investing in advanced technology such as automated cutting systems or precision placement machines that minimize excess material usage during production runs of circuit board manufacturing. Regularly reviewing inventory management practices can also help identify slow-moving items that may lead to obsolescence if not used promptly—thus reducing unnecessary waste.
Lastly, fostering a culture of continuous improvement among your team encourages innovative ideas on how to reduce scrap rates further during PCB board assembly processes. Engaging employees at all levels ensures everyone feels invested in creating a more efficient operation while contributing valuable insights into potential areas where material waste can be minimized effectively.
Outsourcing vs. In-House PCB Assembly
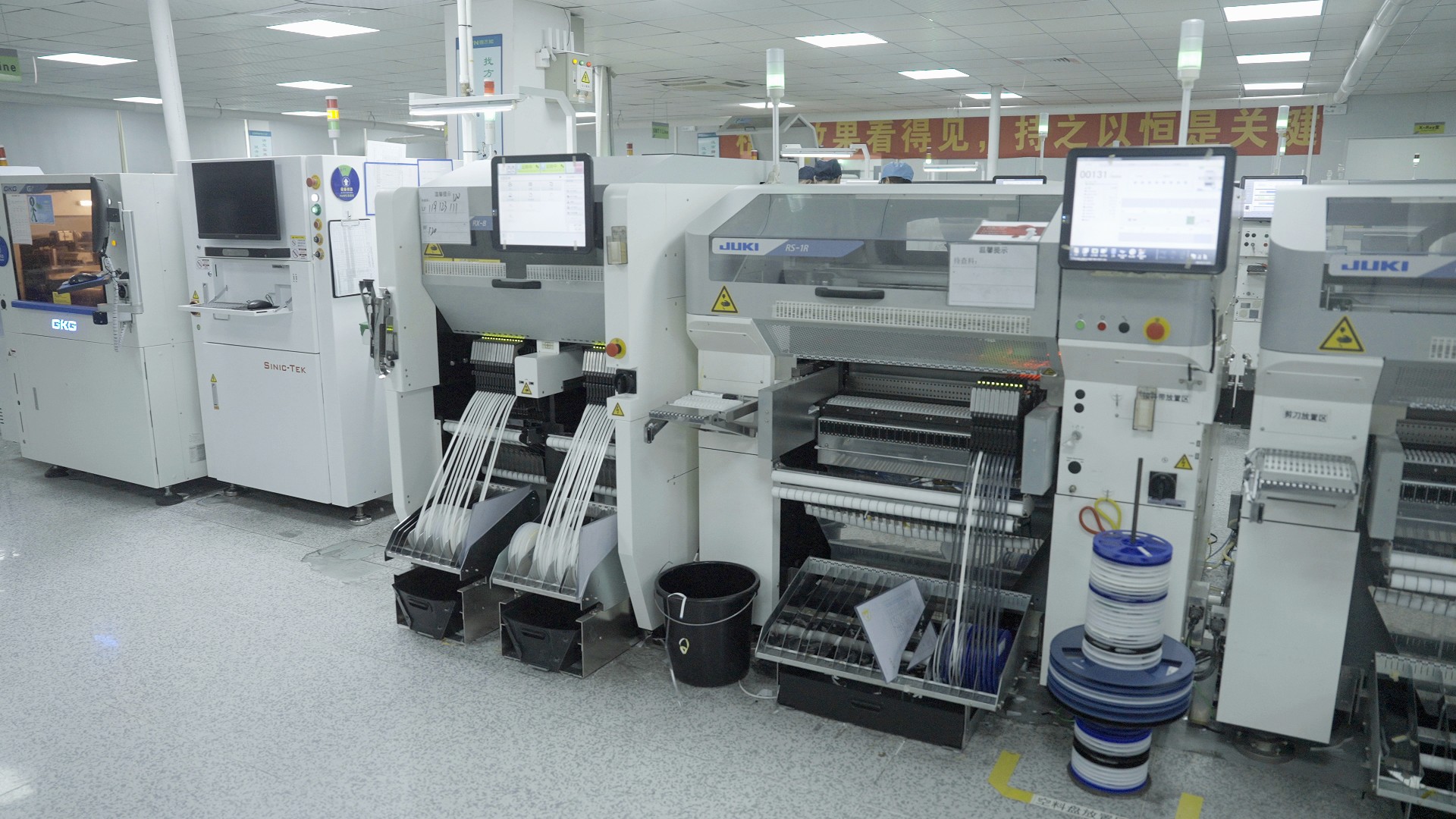
When it comes to PCB assembly, companies often face a crucial decision: should they outsource their circuit card assembly or keep it in-house? Each option has its own set of advantages and drawbacks that can significantly impact the overall efficiency and cost-effectiveness of PCB manufacturing. Understanding these factors is essential for any business looking to optimize their PCB board assembly processes.
Cost-Benefit Analysis of Outsourcing
Outsourcing PCB assembly can lead to significant cost savings, especially for smaller businesses that may not have the resources to invest in advanced equipment or skilled labor. By partnering with a dedicated PCB board manufacturer, companies can leverage economies of scale and benefit from reduced material costs due to bulk purchasing. However, it's crucial to weigh these savings against potential risks such as quality control issues and longer lead times that can arise when relying on external suppliers for circuit board manufacturing.
Additionally, outsourcing allows companies to focus on their core competencies while leaving the complexities of PCB assy to specialized manufacturers. This can free up valuable time and resources, enabling businesses to innovate and expand without getting bogged down in production logistics. Nevertheless, it's vital for companies considering this route to conduct thorough research into potential partners, ensuring they choose a reliable manufacturer that maintains high standards in quality and service.
Advantages of In-House PCB Assy
On the flip side, managing your own circuit card assembly offers several distinct advantages that can be particularly appealing for larger organizations or those with unique product requirements. One major benefit is the increased control over the entire manufacturing process—from design through production—which often leads to enhanced quality assurance in PCB board assembly. With direct oversight, companies can quickly address any issues that arise during production without waiting on external communication.
Moreover, having an in-house team dedicated to PCB manufacturing fosters a culture of innovation and agility within the organization. Teams are better positioned to iterate designs rapidly based on real-time feedback from testing phases or customer input. This capability not only shortens development cycles but also enhances responsiveness in adapting products according to market demands.
Finding the Right Balance in PCB Board Assembly
Ultimately, the decision between outsourcing and in-house circuit board manufacturing isn't black-and-white; many businesses find success by striking a balance between both strategies. A hybrid approach allows organizations to utilize external resources for high-volume production runs while keeping critical projects or prototypes within their own facilities for more hands-on management and innovation opportunities.
This strategy enables flexibility—companies can scale operations up or down based on demand without overcommitting resources either way. By carefully analyzing project needs, budget constraints, and long-term goals related to quality control and turnaround times, businesses can craft an effective approach tailored specifically for their unique circumstances within the realm of PCB assy.
Conclusion

In the ever-evolving landscape of PCB assembly, understanding the intricacies of costs and quality is paramount for success. As we have explored, effective strategies can significantly enhance the cost-efficiency of circuit card assembly while maintaining high standards. By focusing on quality and leveraging technology, manufacturers can navigate the complexities of PCB manufacturing with greater ease.
Key Takeaways for Cost-Effective PCB Assembly
To achieve cost-effective PCB board assembly, it’s essential to prioritize strategic planning and supplier selection. Choosing the right PCB board manufacturer can lead to significant savings through optimized processes and material choices. Additionally, embracing automation and advanced equipment in circuit board manufacturing can streamline operations, further reducing costs without compromising quality.
The Role of Quality in Reducing Long-Term Costs
Quality plays a critical role in minimizing long-term expenses associated with PCB assy. Investing in high-quality materials and processes not only enhances product reliability but also reduces the likelihood of costly errors and reworks down the line. By fostering a culture that prioritizes quality at every stage of pcb manufacturing, companies can ensure sustainable growth and profitability.
Future Trends in PCB Manufacturing Costs
Looking ahead, several trends are poised to shape the future landscape of pcb assembly costs. The increasing adoption of sustainable materials will likely drive innovation while also impacting overall production expenses positively. Furthermore, advancements in technology—such as AI-driven automation—will continue to redefine efficiency benchmarks within circuit board manufacturing, paving the way for more cost-effective solutions.